SPRING ENERGIZED SEALS
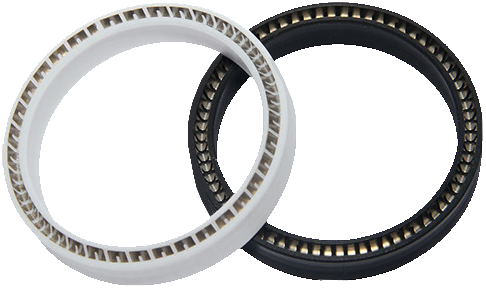
OVERVIEW
Sigma Seals & Gaskets manufactures spring energized seals and sealing systems to fit your design specifications. We make seals in whatever size you need, using the materials of your choice. Our experienced team of engineers can assist in material selection to meet your needs.
Whether you want a lip seal, piston seal, rod seal, or face seal, Sigma Seals & Gaskets will create the seal to meet your exact specifications
Design Considerations
Spring energized seals are designed so that the tension of the internal spring is sufficient to hold the seal firmly in place, even when the system is not active. In pressurized systems, the pressure of the fluid (either liquid or gas) provides a supplementary force that creates an even tighter seal between the two sealing surfaces.
To help ensure that a spring energized seal functions as required, it is important to select materials for the spring and the seal that are appropriate for the expected operating conditions. High temperatures or corrosive fluids require one of our high performance materials.
Spring design can also play a part. Sigma Seals & Gaskets uses three types of springs: v-springs, helical coil springs, and canted coil springs.
We can help you design the right seal for your specifications. Contact our experienced engineers to get expert feedback on your specialized needs.
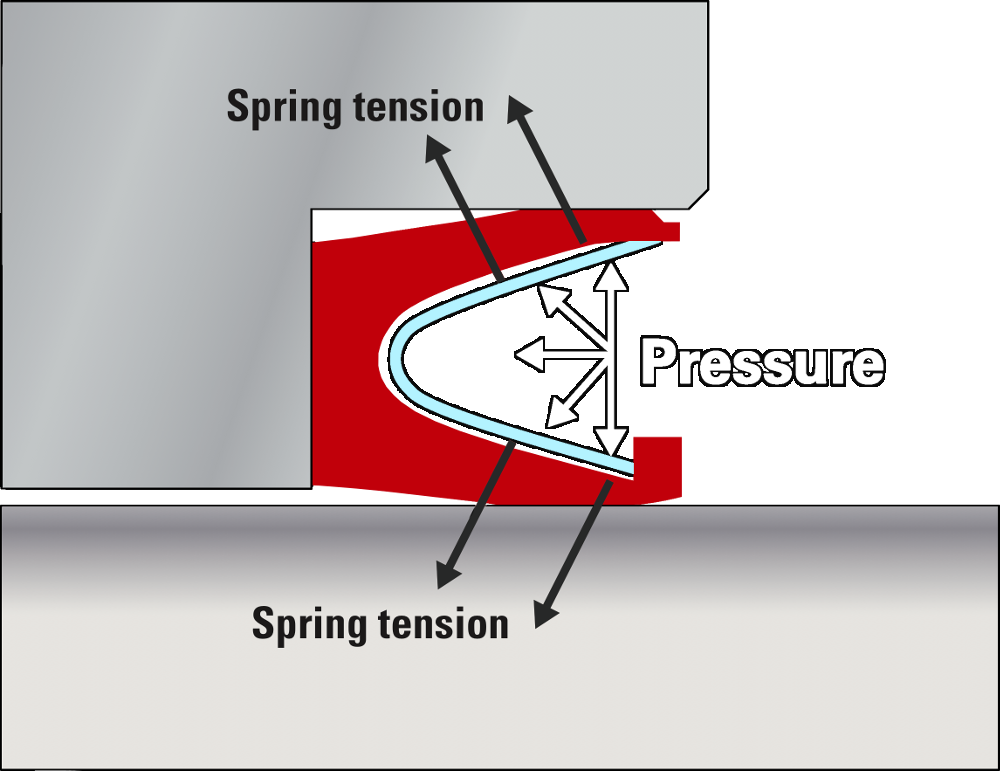
Tension from the spring and pressure from the external gas or liquid combine to hold the seal against the rod
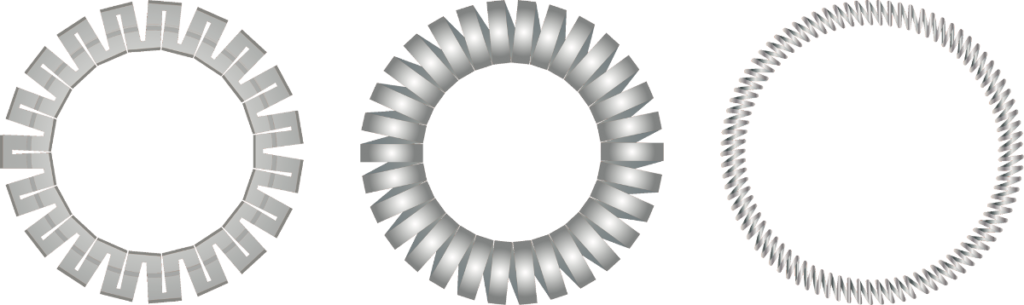
The three types of springs –
v-springs, helical coil, & canted coil
Seal Jacket Material | Temperature Range (°F)* | Comments |
---|---|---|
Virgin PTFE | -400 to 450 | The most suitable material for cryogenic service; also useful for light gases and light duty applications. |
Graphite-filled PTFE | -320 to 475 | Excellent choice when lubricants cannot be added (the graphite acts as a dry lubricant). |
Glass-filled PTFE | -350 to 500 | Has high compressive strength, excellent chemical resistance, low creep, good compressive strength, and good wear resistance under load and permanent deformation. |
Glass/moly-filled PTFE | -250 to 550 | Useful in high-speed applications and in applications that use hardened components. |
Carbon/graphite-filled PTFE | -320 to 475 | Has good wear and creep resistance; good for applications that require dynamic sealing at extreme temperatures. |
Calcium fluoride-filled PTFE | -350 to 500 | Has excellent compressive strength, excellent chemical resistance, and improved wear resistance under load and permanent deformation. |
Carbon/graphite/PPS-filled PTFE | -200 to 550 | A heavy-duty material, excellent for non-lubricated service at high temperatures and pressures. |
UHMW-PE | -320 to 200 | An FDA-approved material with high wear resistance. |
PEEK | -100 to 550 | A high-modulus material with excellent thermal and mechanical properties. Useful for ultrahigh pressure applications. |
* Temperature ranges given here are approximate; the values relevant to any particular situation depend upon the application. If in doubt, ask us—we will help you design a backup ring to meet the temperature tolerance needs of your system.
Spring Material | Maximum Temperature (°F) | Chemical & Corrosion Resistance | Typical Uses |
---|---|---|---|
301 Stainless steel | 500 | + | General purpose |
316 Stainless steel | 500 | ++ | General purpose |
Hastelloy® C-276 | * | +++ | Highly-corrosive or high-temperature environments |
Elgiloy® | * | ++++ | Applications that are simultaneously highly corrosive and high temperature; NACE- approved material for salt water applications |
* When a spring is made from one of these alloys, the seal material is the limiting factor for service temperature.
Applications
- Static or dynamic applications
- High or low pressures
- High or low temperatures
- Usable in corrosive environments
- Use in corrosive environments
Benefits
• Fabricated from custom materials to meet the exact needs of the application
• One-piece design greatly simplifies installation and replacement
• Directly replaces other types of seal in the same size gland (no re-machining or redesign required)
• Designed not to undergo spiral (twisting) failure
• Extremely resistant to extrusion
• Usable with comparatively large extrusion gaps
• Provides prolonged service
• Requires minimum maintenance
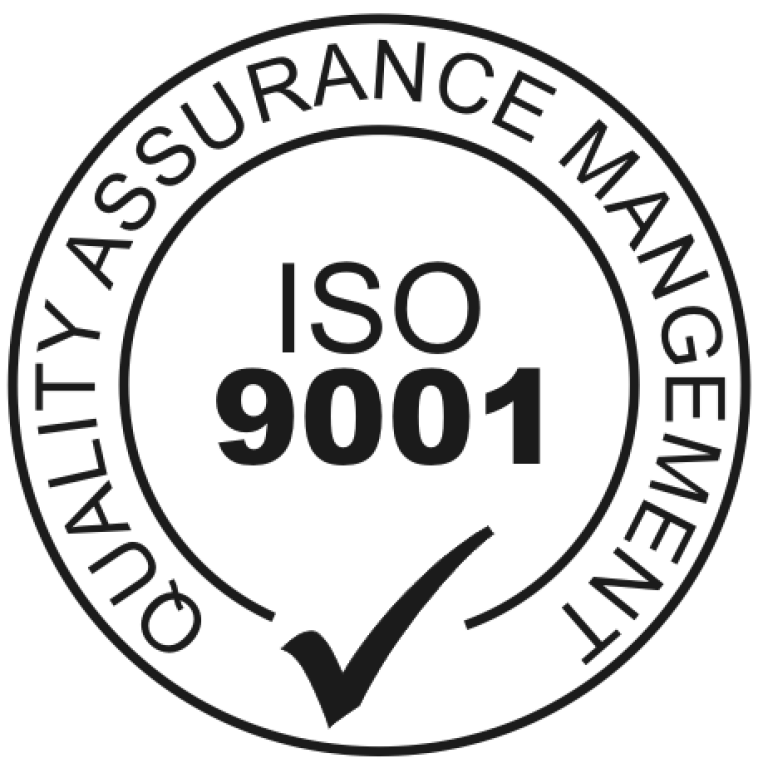
QUALITY GUARANTEE
Sigma Seals & Gaskets specializes in quality elastomeric products. With over 100 years of engineering expertise we are dedicated to offering the highest quality elastomeric products as well as other products. For your custom quality product design or reverse engineering, our exemplary service and efficient production ensures prompt deliveries coupled with outstanding service.
FREE QUOTE
Do you need help with a product? Fill out this form to get in touch.